There are many debate amount boaters and do it yourself lovers of good old boats. One that I have heard many times has to do with plumbing and whether or not it is better to have flexible hose or rigid plumbing. Being on our third good old boat refit, I have some opinions I have started to form over time and this blog post is going to be my best attempt to providing the pros and cons of each as well as my conclusions and ultimately what I chose to do on our latest refit and more importantly why.
For the purpose of this post, I am going to keep the discussion primarily focused on gray water (sinks, showers, etc) and not waste water (black water) or fresh water for your drinking water supply. We have written blog posts and done youtube videos on our selection of PEX for our fresh water system and what all the merits were of that.
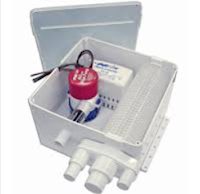
DreamChaser is equipped with a forward head that has a standalone shower/tub combo as well as the sink. The sink was plumbed directly overboard through a small seacock under the head floor. The shower was plumbed to the bilge. I would absolutely NOT recommend doing this and upon moving aboard, we agreed that we would not shower in the forward head until this was resolved. The primary issues with draining a shower into the bilge are that if there is hair that works it’s way down into the bilge and you have an impeller based bilge pump the hair can and will wrap around the shaft and render the bilge pump useless. Additionally all that soap scum what you rinse off of you ends up becoming a nasty smelly build up in the bottom of your bilge.
We knew we wanted to control liquid in the bilge and to do that we really needed to not only route any shower drains into a sump, but also wanted to make sure that the air conditioner condensation also went into a sump. Unfortunately that was also draining into the bilge on DreamChaser. There were small independent Condensate sumps but they were not operational.
The decision was made to install a shower sump that would take inputs from the forward shower, forward head sink basin and the forward air conditioner condensation pans and then as the shower sump level in the sump would trigger the pump in it to come on and drain the sump overboard.
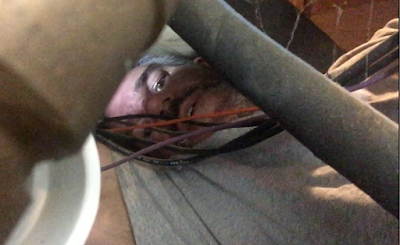 |
Wedged in a hole in the sole and under the floor panel
(Photo taken from under the floor in the head toward the stateroom) |
In order to be successful, we also realized that we would need to install a strainer to keep debris from the pump as well as locate it in a place that made cleaning the filter something that we would and could get to easily. Over the years we learned that making maintenance easier is one of the best things you can do to ensuring that the maintenance is completed and not ignored.
On DreamChaser, we had 3 seacocks located near the forward head and one was not operational, so we only had 2 at our disposal. One was used for the Treated waste discharge and the other for the generator water intake. All of these were below the water line and we liked the idea of being able to see the discharge just above the water line for easy inspection.
We have 3 available that are located just aft of midship on the port side. This is about 20 feet or so from the forward head. We contemplated keeping the sump right under the forward head sole and then running a long discharge line of 3/4” thick hose back to the discharge point, but that would require buying and installing about 25-30 feet of hose by the time you factored in the vented loop to avoid siphoning water back into the boat if heeled. This also meant that we would need to install a check valve so that all the water from the vented loop back to the sump did not flow back into the sump when the pump switched off (given the length of hose, this would have been quite a bit of volume of water) The formula for figuring out the volume of a cylinder is Feet * diameter of hose * pie (3.14) which for 20 feet would be X.
this had me at least explore the idea of rigid plumbing. I noticed that the manufactures of the ElectroScan recommend rigid plumbing for their waste discharge system so I started to think that if certain manufactures are calling for it, then done right, it can be a good solution. Done right would be the key here.
What we want to avoid is rubbing on the PVC that would cause Chaffing and allowing the pipe to leak. I chose to use Schedule 40 PVC which is thicker walled and ensured that when we installed it we would ensure it was securely held and if it went through a bulkhead, it was protected to avoid chafe. This was done rather easily by getting some rubber sheets designed to make replacement gaskets (we picked ours up at an Ace Hardware) and I would wrap a 1” wide strip of this around the pac pipe where it went through a bulkhead so it was a snug fit and kept it from rubbing on the hole that is passed through.
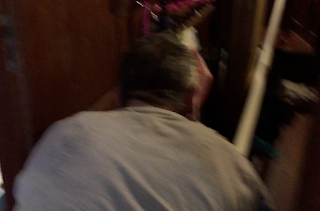 |
Feeding rigid PVC under the sole |
We decided that we would locate the sump very close to the through hull which meant we had to make a much longer run of the wider pipe (the inlet is 1.5” diameter and the output line is 3/4”) but since we were buying rigid Schedule 40 PVC a 10 foot section of PVC costs less than 1 foot of the flexible line from a marine chandlery.
It is important that you follow all directions for PVC assembly like keeping the cuts square, cleaning the mating surface, using the correct PVC glue, etc but if you cut and dry fit your pieces first it is not a difficult job. In our case I think I struggled more with getting in and out of the tight space under the double berth sole so that I could get 1 hand on the bottom side of the shower drain to connect things. As a side note both of my shoulders and my right hip felt sore and bruised the next day after doing the work and I am sure it was from the very awkward positions required. I was actually shocked that Deb didn’t take a picture of me where you could only see my thighs and legs coming up out of the floor and from the waste up I was skootched up under the sole. I even had to put one arm over my head as I worked myself into that spot because once in there, I didn’t have the room to move my arm into that position between the bulkheads and mast step and other various obstacles in this part of the bilge.
Rather than run 2 separate lines to the sump, I did connect the sink to the shower drain’s large diameter discharge line and then connect it to one of the 4 sump input locations. Because the sump is pre-molded with barbed connections to connect hoses from 3/4” to 1.5”, I had to get a bit creative on connecting the PVC to it. I used a 1” to 1.5” rubber reducer designed for non pressurized lines. Perfect for this application and available at my local home improvement center. This not only accommodates the connection of the rigid PVC to the rigid hose barb, but also allows for a small bit of vibration and flex between the drain pipe and the sump while in any kind of heavy weather.
By using the rigid PVC, it will allow me to locate the sump in a much lower portion of the bilge and make it easily accessible for cleaning. This also reduced the length of flexible hose required for the discharge line which in the end saves money as well.
So half way through this project, I found out I was going to have to leave for Australia for business. The work had to be diverted a bit so we ran the rigid PVC to the bilge where it is still draining into the bilge so that will be a project to finish in the next week now that I am back from Australia. (It has been a crazy busy couple of weeks with work which has slowed the boat projects a little bit) Check out the youtube video below to see some of the footage of the plumbing, my granddaughters first play at indoor paintball and then my flight and trip to Australia. More to come on this project as it wraps up.
If you are receiving this blog via email or on a device that won’t play the embedded video, click this link for the video directly on Youtube. The link is https://youtu.be/FF-FJ78tIaw